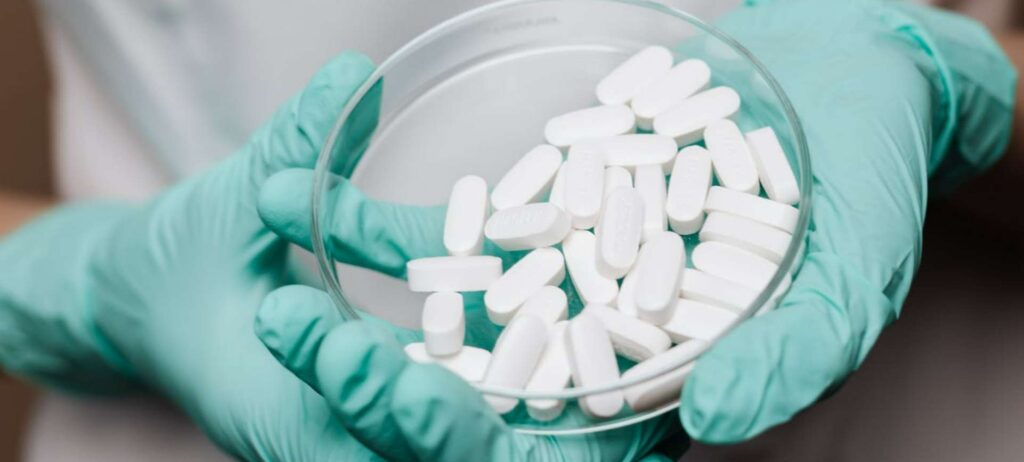
كيف قام مصنع دوائي بتحقيق الربح وتقليل الهدر الانتاجي: دراسة حالة استخدام تقييم OEE وتقنية SMED في حل مشكلات ضغط الأقراص
اتصل بنا مُصنع دوائي مؤخراً وطلب مساعدته في حل مشكلة كبيرة في طاقة ضغط الأقراص. زاد الطلب على المنتج ولكن القدرة لم تتماشى معه، حتى بعد شراء معدات جديدة لتسريع آلة الضغط. بالإضافة الى ان أداء المشغل غير المتسق، وزيادة حجم الوجبات مما أحدث تحديات جديدة وغير مرغوب فيها. تأخرت المشاريع، وتم تفويت موعد التسليم.
الحل الواضح لهذا السيناريو الشائع نسبيًا كان في تطبيق تقييم فعالية المعدات الشاملة، أو OEE، واحدة من أكثر الأدوات فعالية يمكن لمصنعي الأدوية استخدامها لإدارة وتحسين أداء الأصول الرئيسية. يُستخدم OEE بشكل واسع نسبيًا في مجالات مثل التعبئة والتغليف الدوائي، ولكنه يُطبق أيضًا على خطوات التصنيع. يستعرض هذا المقال كيف تم استخدام OEE و SMED لإدارة آلة ضغط الأقراص، مما أدى إلى تقليل زمن التغيير بنسبة 50٪ وانخفاض الانحراف في زمن التغيير بنسبة 75٪.
لا يمكننا الكشف عن اسم الشركة المعنية، ولكن نقدم دراسة الحالة كمساعدة للشركات التي تتطلع إلى استخدام OEE لتحسين عمليات وأداء تصنيع الأدوية.
يقوم OEE، الذي يقيم أداء المعدات وجودة المنتج، بتحديد الفرص للتحسين بشكل منهجي. في هذه الحالة، تم تحديد أوقات التغيير بدلاً من أداء الخط كأكبر سبب للأداء العام والتباين في الإنتاج. ثم استخدمت عناصر من منهجيات Lean و Six Sigma مثل تحديد المشكلة، وقياسها، وتحليلها، وتحسينها، والتحكم فيها (DMAIC)، وتبديل القوالب في دقيقة واحدة (SMED) للقضاء بشكل منهجي على الفاقد من عملية التغيير دون التضحية بالجودة أو تعريض الامتثال للخطر. بالإضافة إلى ذلك، تم استخدام العمل الموحد، والمراقبة المباشرة للخط، وتحليل أسباب الجذور، ومراقبة العملية الإحصائية للتحكم في التباين ووضع أساس جديد لعملية التغيير.
كانت إحدى أول الإجراءات هي قياس “الحالة الحالية” بدقة. كما هو الحال مع أي قطعة رئيسية من المعدات، يُطلب قياس استخدام المعدات. أفضل مقياس لذلك هو OEE لأنه يوفر معلومات محددة حول مكان الهدر. بالنسبة للقياسات الشائعة مثل وقت التشغيل، وحدات الإنتاج، وسرعة الإنتاج، يساعدنا OEE في فهم ما يمكن أن يكون من الممكن إنتاجه ومكان مصادر عدم الكفاءة.
يتألف OEE من ثلاث فئات رئيسية: التوفر، والأداء، والجودة.
التوفر هو الوقت الذي يتم فيه تشغيل المعدات مقارنة بالوقت الذي كان يمكن أن تكون فيه. يعكس معدل التوفر المنخفض وقت التوقف من: التغييرات، والتنظيف، وتغييرات الورديات والغداء، والفواصل، إلخ.
الأداء هو الكمية المنتجة مقابل الكمية المحتملة المنتجة بمعدل تشغيل معين. يعكس معدل الأداء المنخفض التغيرات في السرعة من: سرعة الخط البطيء، ووقت التوقف الخاص بالماكينة، ونقص العمالة، إلخ.
الجودة هي كمية المنتج الجيد مقابل المنتج الإجمالي المنتج. يعكس معدل الجودة المنخفض العيوب من: إعادة العمل.
يمكن معالجة التوفر، والأداء، والجودة بشكل فردي أو مشترك من أجل تحسين الإنتاجية العامة. (ملحوظة: TEEP، الإنتاجية الكلية الفعالة للمعدات، تكون مساوية لـ OEE عند التشغيل على مدار 24/7. لا يتم مناقشة TEEP هنا.)
في صناعة الأدوية، تحتوي العديد من المعدات على أوقات إعداد طويلة لأنه يجب تفكيك المعدات، وتنظيفها، وإعادة إعدادها وفقًا لمعايير cGMP. يمكن أن يمثل هذا الفاقد من الوقت خسارة كبيرة في الإنتاجية (جزء التوفر من OEE).
التغيير الرئيسي الأول هو الطلب من المشغلين قياس أوقات التغيير إلى أقرب ساعة ونشر هذه الأوقات على جدول في المنطقة، بمجرد اكتمال كل عملية تغيير. بالإضافة إلى ذلك، تم تفريق الوقت الإجمالي للتغيير إلى ثلاث مكونات زمنية منفصلة: 1) تفكيك؛ 2) تنظيف؛ 3) إعداد.
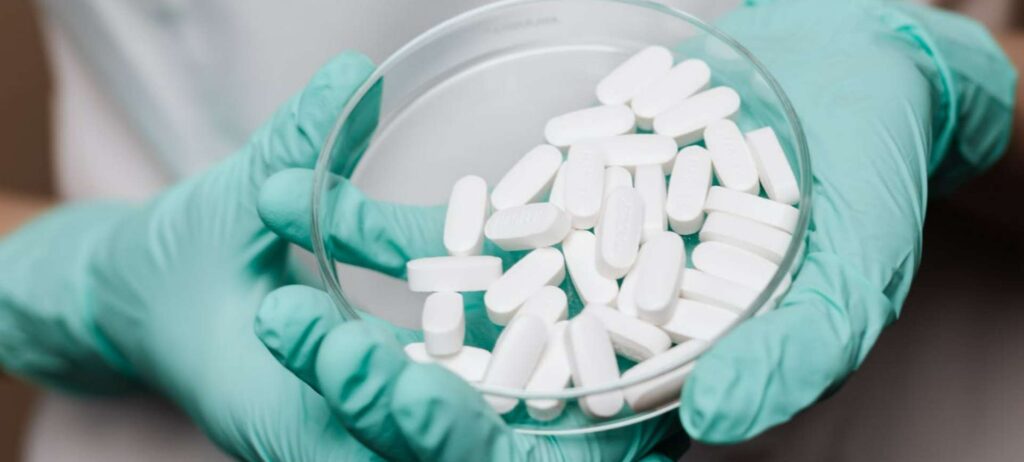
زمن التفكيك + زمن التنظيف + زمن الإعداد = وقت دورة التغيير الإجمالي.
تم استخدام المراقبة المباشرة ودراسات الزمن لقياس وقت الدورة وإنشاء خريطة عملية لكل هذه المكونات الزمنية. تمثلت هذه الخريطة العملية في تحديد خطوة بخطوة لكل نشاط ضروري لإكمال عملية التغيير.
مع مساهمة المشغل، تم تصنيف هذه الإجراءات بعد ذلك كالتالي:
أ) إضافة قيمة؛
ب) الفاقد (وفقًا لأسباب الهدر السبعة المعروفة في نظام الإنتاج الرشيق)
ج) إضافة قيمة للعمل (الأنشطة التي لا تضيف قيمة ولكنها ضرورية للعمل، مثل ملء سجلات الدفعة).
بعد ذلك، تركز الفريق على إيجاد طرق للقضاء على الفاقد وتقليل الوقت المستغرق في الأنشطة التي تضيف قيمة للعمل.
يتكون الفاقد في هذه الحالة بشكل رئيسي من هدر الحركة (البحث عن العناصر) والمعالجة الزائدة (تنظيف متكرر للأدوات وتوضيح التعليمات). الأنشطة التي تضيف قيمة للعمل هي في المقام الأول متعلقة بالوثائق. من المهم أن ندرك أن الوثائق مهمة للحفاظ على الامتثال التنظيمي، لكنها نشاط لا يضيف قيمة. يجب بذل الجهود لجعل الوثائق بسيطة ومضمونة من الأخطاء قدر الإمكان. هذا يقلل من تباين وقت الدورة حيث يمكن أن تؤثر أخطاء الوثائق والتحقيقات غير النموذجية بشكل كبير على إصدار المنتج ووقت الدورة الإجمالي.
كيف قمنا بتحليل وحل مشكلة الشركة
استخدم تحليل “5 لماذا” بسيط لكل من الهدر المحدد لتطوير الأسباب الجذرية وتجميع الحلول. مثال على تحليل “5 لماذا” للأدوات المفقودة كما يلي.
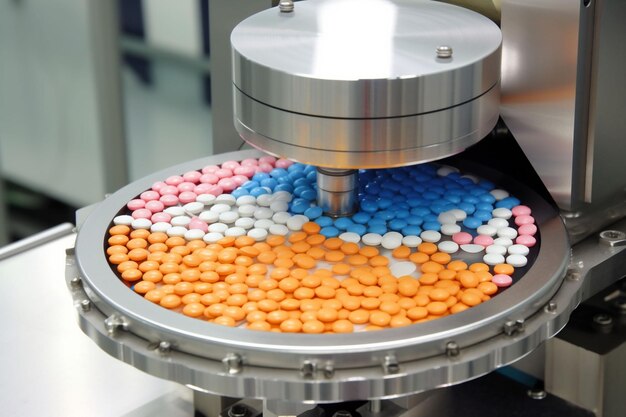
خلال عملية التغيير هذه، لوحظ ان الأدوات مفقودة أو تفقد بشكل متكرر. الشائع ان كل مشغل عليه الاحتفاظ بمجموعة خاصة من الأدوات، غالبًا غير كاملة، وإنشاء وصيانة موقع تخزين مشترك لم يكن قد اعتبر.
والأهم من ذلك، الإجراء القياسي لم يوثق “أفضل الطرق” لإكمال العمل. بالإضافة، قدم الإجراء القياسي مرونة زائدة للمشغلين. نتيجة لذلك، قام المشغلون بإكمال العمل كما يرون مناسبًا.
استخدمت تقنية “5 لماذا” لكل من الهدر المحتمل لتحديد الأسباب الجذرية. كانت أكثر الأسباب الجذرية شيوعًا للأوقات الطويلة والمتغيرة بشكل كبير لدورة العمل هما:
1. نقص التواصل بين الورديات
2. نقص في خطة العمل القياسية.
تم بعد ذلك استخدام تحليل SMED (تبديل القوالب في دقيقة واحدة) لتقييم كل من الأنشطة ضمن كل من مكونات الزمن. يعد SMED أداة Lean توفر طريقة لتقليل أوقات التهيئة/التغيير. يتم تصنيف الأنشطة على أنها داخلية، خارجية، أو غير ذات قيمة مضافة. الأنشطة الداخلية يجب أن تنجز خلال فترة التغيير (الأنشطة على المسار الحرج)، بينما تُجرى الأنشطة الخارجية قبل بدء التغيير. يتم إلغاء الأنشطة غير ذات القيمة المضافة. بعض الأمثلة هي:
• داخلية: استخدام قطع الغيار، حركة العربة، تنظيف الغرفة
• خارجية: تنظيف الأدوات، حركة الأجزاء
• غير ذات قيمة مضافة: ملء قائمة التفكيك، تحميل الرفوف المتعددة، البحث عن المواد.
من أجل تحسين عملية التغيير، تم تدبر حلول تعالج نقص التواصل بين الورديات ونقص في خطة العمل القياسية لكل من مكونات الزمن: التفكيك، والتنظيف، والإعداد.
على وجه الخصوص، تم استخدام العمل القياسي، أداة Lean، لتحديد بوضوح إجراءات كل مشغل. العمل القياسي يحدد إجراءات كل مشغل وترتيبها. بفضل العمل القياسي، تمكن الفريق من تزامن إجراءات عدة مشغلين، مما يضمن أن العمل يتم بطريقة فعالة للغاية وقابلة للتكرار. يقلل العمل القياسي من التباين وبالتالي يعزز السلامة والجودة والإنتاجية.
تم تجريب الحلول وتحققت الأسباب الجذرية خلال عدة عمليات تغيير مع نتائج مثيرة للإعجاب – تم تقليل الأوقات الإجمالية للتغيير إلى 17.5 ساعة، بنسبة تقليل تزيد عن 50٪. تم تقييم المخاطر وأظهرت عدم وجود مخاطر محتملة للمنتج أو الGMP.
مرحلة التحكم: كيف أحافظ على هذه النتائج
غالبًا ما يتمكن مشاريع التحسين من تحقيق أهدافها، على الأقل في البداية؛ ومع ذلك، يمكن أن يتدهور الأداء مع الوقت. من أجل منع التراجع الإداري، قمنا بتدريب إدارة المنطقة على SPC، أو التحكم الإحصائي في العمليات.
يستخدم SPC الأساليب الإحصائية لمراقبة أداء العملية. تساعد هذه الأداة الإدارة في اكتشاف عندما يبدأ أداء العملية في “الانحراف”.
تم تنفيذ رسم تحكم SPC اليدوي كجزء من مشروع التغيير ويقع حاليًا على لوحة التصور في منطقة التشغيل. تم تدريب المشغلين على تحديث وصيانة مقاييس زمن الدورة بعد كل عملية تغيير وتشجيعهم على تقديم اقتراحات للتحسين للمشرفين.