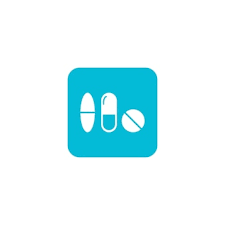
تحليل الأسباب وراء هدر المواد: استخدام البيانات لتحليل أداء الخط الإنتاجي
استكشف تقنيات حساب ومراقبة هدر المنتج في صناعة الأدوية، مع تحليل مفصل لكل مرحلة في عملية التصنيع. اكتسب المهارات الضرورية لتحقيق الإنتاجية المثلى وتقليل الفقدان على الخط. اقرأ لتفهم كيف يمكنك تحسين أداء إنتاجك والحفاظ على جودة المنتج النهائي.
يعد فهم هدر المنتج أمرًا أساسيًا لتحقيق أقصى قدر من الإنتاجية في صناعة الأدوية. نتعرف هنا على كيفية حساب الإنتاجية بدقة وتقدير هدر المنتج في كل مرحلة من مراحل التصنيع.
يتم حساب فاقد (هدر) الخط خلال كل مرحلة من مراحل التصنيع لضمان أن العائد أو فقدان الخط يكون ضمن النطاق الموصى به. جميع صناعات الأدوية لديها إجراءات تشغيل قياسية (SOP) تعرف الانتاجية النهائية لمنتج صيدلاني بعد التعبئة والتغليف.
تقاس الانتاجية عادةً بالنسبة المئوية وهو نسبة كمية المنتج قبل التصنيع إلى كمية المنتج بعد التصنيع أو نسبة كمية المنتج النظرية إلى كمية المنتج العملية، وصيغته كما يلي:
الانتاجية = كمية المنتج بعد التصنيع ÷ كمية المنتج قبل التصنيع × 100
أو
الانتاجية = الكمية الفعلية ÷ الكمية النظرية × 100
مثال
في صناعة الأدوية، تم تصنيع وجبة من الأقراص بحجم قياسي يبلغ 50 كيلو جرام بعد عملية القياس و49.0 كيلو جرام بعد عملية التلبيس.
قم بحساب انتاجية هذه الوجبة
من خلال استخدام الصيغة أعلاه، أضف القيم كما يلي:
العائد = 49 ÷ 50.0 × 100 = 98.0%
إنتاجية الوجبة هو 98.0%.
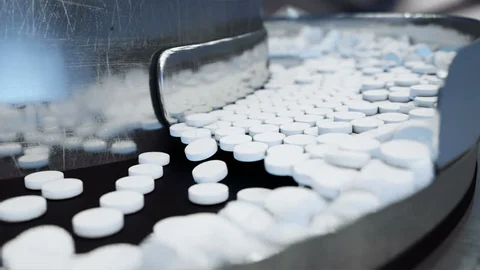
ما هو فقدان (هدر) الخط؟
هدر الخط هو قياس فقد المواد خلال كل مرحلة في عملية التصنيع. قد يحدث فقدان الخط ابتداءً من مرحلة الخلط الاولي وحتى إرسال المنتج النهائي.
الإنتاجية = كمية المنتج قبل التصنيع -كمية المنتج بعد التصنيع
على سبيل المثال، إذا تم تصنيع دفعة من الأقراص بحجم دفعة قياسي يبلغ 60 كيلو جرام بعد عملية التوزيع و59.5 كيلو جرام بعد عملية التلبيس. إذا، فإن فقدان المنتج هو 0.500 كجم.
أسباب فقدان المادة على الخط
قد يحدث فقدان الخط بسبب الأسباب التالية وفي المراحل التالية:
أثناء عملية الخلط، قد يحدث انزلاق لبعض المواد مع الهواء العائد بسبب البيئة الغبارية.
قد تلتصق بعض المواد بالآلات أثناء عملية الخلط.
قد تلتصق بعض المواد بأكياس البولي إثيلين.
بسبب تسرب نتيجة عطل أو مشكلة في احكام اغلاق جهاز الخلط
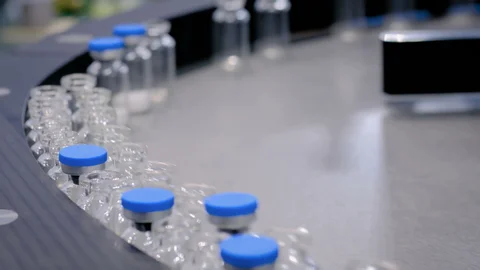
التحثير
أثناء عملية التحثير، قد يحدث فقدان الخط بسبب الأسباب الرئيسية التالية:
– قد تلتصق بعض المواد بأكياس البولي إثيلين عند إزالتها من الأكياس.
– فقدان المواد أثناء الغربلة بسبب البيئة الغبارية.
– أثناء الخلط والعجن، قد تلتصق بعض المواد بجدران وشفرات المحثرة.
– خلال عملية التحثير، يتم حساب الهدر أو فقدان الخط بعد مرحلة التجفيف والخلط النهائي.
مثال
تم خلط وجبة من الأقراص بوزن إجمالي قياسي يبلغ 75 كجم. تم تصنيعها بطريقة التحثير الرطب وتجفيفها في FBD. بعد التجفيف، يكون وزن المنتج 74.0 كجم. وزن القرص 750 ملغ، وعدد الأقراص 100،000 قرص. قم بحساب إنتاجية الوجبة وفقدان الخط للمنتج.
أولاً، سنقوم بحساب انتاجية المنتج بواسطة الصيغة التالية:
الإنتاجية=كمية المنتج بعد التجفيف/كمية المنتج قبل التجفيف*100
الإنتاجية = 98.66%
الآن حساب فقدان الخط بواسطة الصيغة التالية:
هدر الخط= كمية المنتج قبل التجفيف -كمية المنتج بعد التجفيف
هدر الخط=1 كغ
بعد الخلط، يتم حساب الانتاجية وفقدان الخط بنفس الطريقة المذكورة أعلاه.
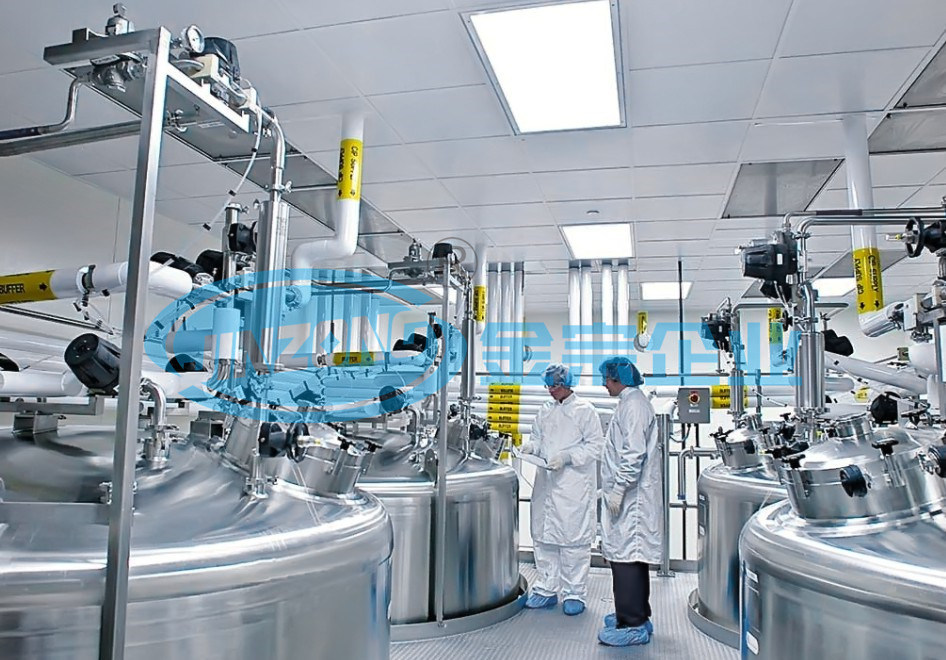
مثال
تم غربلة المنتج المذكور أعلاه باستخدام جهاز الغربلة الهزازة وخلطه في الخلاط. بعد الخلط، يصبح وزنه النهائي 73.7 كغ. قم بحساب العائد وفقدان الخط للمنتج.
أولاً، سنقوم بحساب انتاجية المنتج:
الإنتاجية=73.7÷75×100
=98.26%
يتم حساب فقدان الخط كالتالي:
=75-73.7=1.3 كغ
بعد التجفيف، إنتاجية الوجبة هي 98.66٪ وفقدان الخط هو 1.0 كجم. بعد الخلط النهائي، يتم حساب انتاجية المنتج وفقدان الخط بنفس الطريقة المذكورة أعلاه لجميع مراحل التحثير ابتداءً من الغربلة وحتى الخلط النهائي، لذلك العائد الإجمالي وفقدان الخط بعد اكتمال عملية التحثير هو 98.26٪ و1.3 كجم على التوالي.
عملية الكبس (ضغط المضغوطات)
أثناء مرحلة الضغط، قد يحدث فقدان الخط بسبب الأسباب الرئيسية التالية:
– فقدان المنتج أثناء تحميل المنتج على أصابع المكبس.
– بسبب البيئة الغبارية.
– فقدان المنتج أثناء فحص معلمات العملية.
– في نهاية مرحلة الضغط، يتبقى بعض البودرة أو الحبيبات في المغذي أو القالب ولا يمكن ضغطها.
– قد يتبقى بعض البودرة أو الحبيبات في الهزاز
مثال
تم تسليم المنتج المحثر المذكور أعلاه بوزن 73.7 كغ إلى غرفة المكبس وبعد الضغط، أصبح وزن الوجبة 73 كجم. قم بحساب إنتاجية المنتج وفقدان الخط في مرحلة الضغط.
استخدم الصيغة التالية:
الإنتاجية= كمية المستحضر بعد الكبس ÷ كمية المنتج قبل الكبس ×100
= 73 ÷ 73.7 ×100
=99.05%
يتم حساب فقدان الخط على النحو التالي:
=73.7-73
=0.7 كغ
النتائج:
أثناء مرحلة الضغط، العائد هو 99.05٪ وفقدان الخط هو 0.7 كجم.
إذا أردنا حساب الانتاجية الإجمالية وفقدان الخط لمرحلتين التحثير ومرحلة الضغط، يتم حسابها على النحو التالي:
الإنتاجية=73 ÷75 ×100
=97.33%
يتم حساب فقدان الخط كالتالي:
فقدان الخط=كمية المنتج قبل التحثير – كمية المنتج بعد الكبس
= 75-73
لذا، فإن فقدان الخط لمرحلتين هو 2.0 كغ والانتاجية هي 97.33٪.
التلبيس:
في تلبيس الأقراص، يتم اضافة وزن إضافي على كل قرص عن طريق رش محلول أو تعليق للبوليمر بحيث يتم زيادة وزن المنتج.
قد يحدث فقدان الخط في عملية التلبيس بسبب:
– إهدار سائل التلبيس من خلال منفذ الهواء.
– درجة حرارة الورود العالية ومعدل الرش المنخفض يؤديان إلى فقدان المواد.
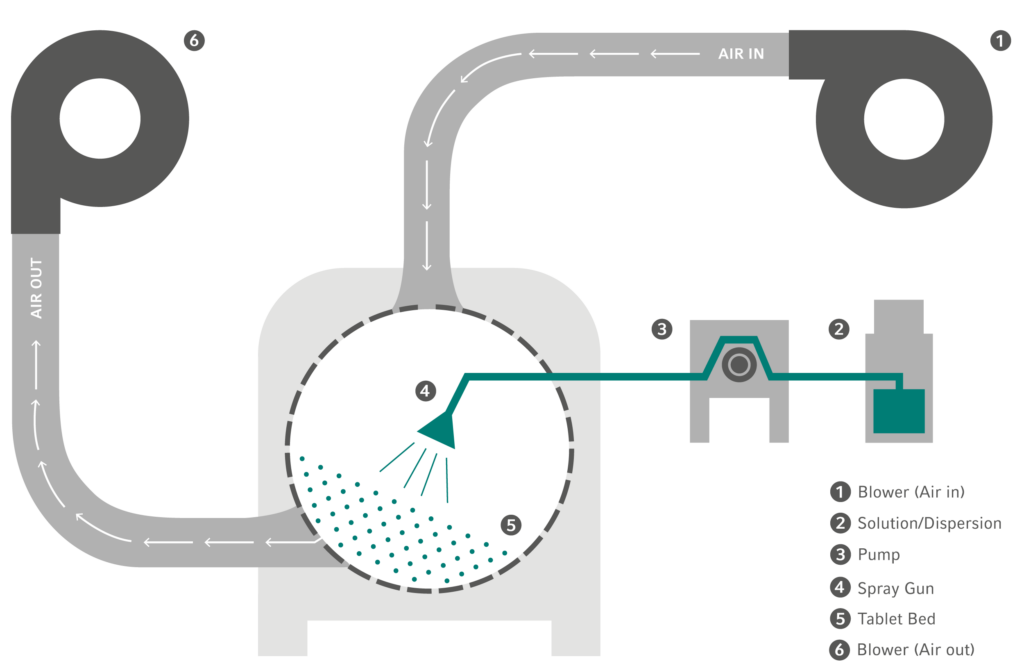
مثال
تم استخدام سائل تلبيس لتغليف دفعة الأقراص المذكورة أعلاه بمقدار 2 كغ. حجم الوجبة 100،000 وتم استلام 73 كجم للتلبيس. عدد الأقراص لـ 73 كغ هو:
عدد الأقراص = 73*1000*1000/750
=97333 قرص
مواد التلبيس لكل قرص هي:
=2*1000*1000
=20 ملغ
لذا بعد التلبيس، نظريًا، يجب أن يكون وزن كل قرص:
=750+20
=770 ملغ
لكن بعد التلبيس، تم الحصول على 764 ملغ لكل قرص، وهو يعني فقدان 6 ملغ لكل قرص.
حساب الانتاجية لـ 100,000 قرص:
=770*100000
=77 كغ
ووزن الوجبة بعد التلبيس 74.362 كغ
الإنتاجية= 74.362÷77 × 100
=96.574 %
فقدان الخط= 77-74.362
=2.638 كغ
يمكننا أن نرى أنه مع زيادة عدد مراحل عملية التصنيع، تقل الانتاجية ويزيد فقدان الخط.
من التحثير إلى التلبيس، الانتاجية الإجمالية هي 96.574 وفقدان الخط هو 2.638 كغ
من خلال فحص عناصر هدر المنتج وتحليل كل مرحلة في عملية التصنيع، يمكن للشركات في صناعة الأدوية تحسين إدارة الإنتاج وتحقيق نتائج متميزة. تطبيق استراتيجيات فعالة للحد من هدر المنتج يسهم في تعزيز الجودة والكفاءة العامة في الإنتاج.
المرجع المستخدم: