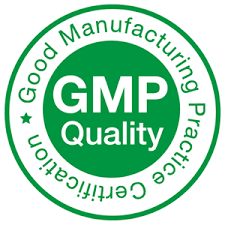
الاستفادة من الإحصائيات وتجنب الافتراضات اثناء القيام بالتفتيش على ممارسات التصنيع الجيدة في صناعة الادوية
اكتشف كيف يمكن استخدام الإحصائيات وتحليل جذور السبب للتصدي لأخطاء التصنيع المتكررة وتحسين جودة المنتجات والامتثال للمعايير بفعالية.
الاستفادة من الإحصائيات: قد يكون أول خطوة مهمة في تجنب أخطاء التصنيع المتكررة هو نشر الإحصائيات المتعلقة بالمشاكل الشائعة بشكل دوري. يفعل ذلك بعض البلدان مثل المملكة المتحدة والبرازيل، حيث يتم نشر بيانات توضح النواقص والمشاكل في مجالات مثل تصنيع الأدوية. توفر هذه الإحصائيات نظرة عامة على التحديات والمشكلات التي تواجه الصناعة والشركات.
تحليل جذور السبب: ومع ذلك، لا تكون الإحصائيات العامة مفصلة بما يكفي للتعامل مع المشكلات بشكل فعال. يجب إجراء تحليل جذور السبب لفهم الأسباب الفعلية وراء الأخطاء المتكررة.
التفاصيل : لا تعتبر الإحصائيات وحدها كافية. يجب تسجيل وتحليل كل حالة من الأخطاء بدقة، بما في ذلك تحليل كل العوامل الممكنة التي أدت إلى الخطأ. ذلك يساعد على تفادي الانطباع السلبي من أن الأخطاء دائمًا مرتبطة بالعامل البشري.
استخدام أسلوب “لماذا؟”: قد يساعد أسلوب “لماذا؟” في تحليل الأسباب. يمكن أن يساعد هذا الأسلوب في التفكير بعمق حول الأسباب الجذرية للمشاكل. مثلما يمكن أن يقول الطفل الفضولي: “لماذا حدث الخطأ؟” والإجابة على هذا السؤال تحدد خطوات التصحيح المطلوبة.
عدم الاعتماد على الافتراضات: يجب إجراء تحليل دقيق للبيانات والمعلومات المتاحة، وعدم الاعتماد فقط على الافتراضات في تقدير الأسباب والحلول.
تعزيز التدريب وتحسين العمليات: إذا كانت الأخطاء تتكرر بسبب أخطاء بشرية، يمكن أن تكون التدابير التصحيحية تشمل تدريب الموظفين بشكل أفضل أو تحسين تصميم العمليات.
لا تتجاهل الجوانب التقنية والتنظيمية: يجب أن يتم التحقق من الجوانب التقنية للتأكد من أنها تعمل بشكل سليم.
الاستفادة من التجارب السابقة: يجب أن تكون الأخطاء السابقة درسًا لاستبعادها في المستقبل
أمثلة عملية:
الانحراف الاول: التحليل الصحيح للسبب الجذري:
تبين أن رقم الوجبة لم يتم طباعته بشكل صحيح على عبوة المنتج وتم اكتشاف هذا الخطأ اثناء القيام بالجولة الدورية من قبل عنصر ضمان الجودة. تم استنتاج ان سبب المشكلة هو خطأ بشري من قبل العامل خلال تحليل جذور السبب. وكان يفتقر إلى تقييم أسباب تقنية أو تنظيمية محتملة لهذا “الخطأ البشري”. وكذلك كان الانحراف الثالث من هذا النوع خلال الثلاثة أشهر الأخيرة. (المرجع: دليل EU GMP الجزء الأول رقم 1.4 رقم xiv)
ما هي المشكلة؟
تم ربط نقل رقم الوجبة الخاطئ قبل بدء الإنتاج بعامل بشري دون تحليل مفصل للسبب. نظرًا للنقل اليدوي، كان سبب “الخطأ البشري” واضحًا: بدى أن موظفًا قام بنقل رقم الوجبة بشكل غير صحيح بوضوح. ومع ذلك، وفقًا لدليل EU GMP الجزء الأول رقم 1.4 xiv، يجب التعامل بعناية فائقة مع ما يعرف بـ “الخطأ البشري” ويجب تسجيله كسبب فقط إذا تم استبعاد أسباب تقنية أو عملية أو متعلقة بالنظام أو تنظيمية أخرى. لم يتم التحقق من “صحة” السبب المفترض حتى بعد الانحراف الثالث من هذا النوع خلال الثلاثة أشهر الأخيرة. تم تحديد الخطأ البشري كسبب في كل من هذه الانحرافات، وتم توجيه التدريب التكميلي للموظف المعني كإجراء وقائي.
على الأقل، يجب أن يؤدي تكرار الانحراف إلى تحليل السبب الذي تم التعرف عليه أولاً. إذا ارتكب موظف واحد نفس الخطأ مرارًا وتكرارًا أو ارتكب عدة موظفين نفس الخطأ، قد يكون الأسباب في الواقع تكمن في العملية أو في تدفق العمل
لتجنب هذا الخطأ
عند تحليل الأسباب، تخيل أن لديك طفل فضولي بجوارك يواصل التساؤل قائلاً “لماذا؟”:
الطفل: “لماذا قام الموظف بنقل رقم الوجبة بشكل غير صحيح؟”
أنت: “لأن الموظف لم يستطع التعرف بشكل جيد على رقم الوجبة في اضبارة المستحضر.”
الطفل: “لماذا لم يستطع الموظف التعرف على رقم الوجبة بشكل جيد في اضبارة المستحضر؟”
أنت: “لأن اضبارة المستحضر يمكن أن تكون فقط على الطاولة الجانبية في وقت وضع رقم الوجبة وبالتالي تكون نسبياً بعيدة عن الموظف.”
الطفل: “لماذا الاضبارة بعيدة؟”
أنت: “لأنه لا يمكن وضع وثائق التعليمات على طاولة العمل لأسباب صحية.”
من خلال هذه الطريقة البسيطة في الاستفسار، يمكنك الاقتراب من السبب الفعلي بسهولة نسبية، كما هو موضح مرة أخرى في الشكل .
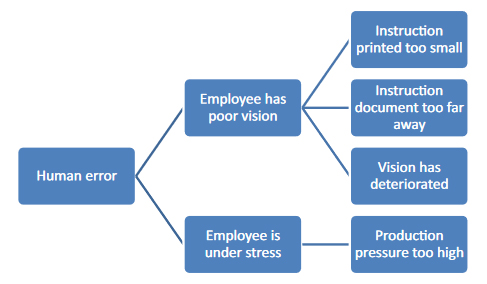
بعد السؤال الخامس “لماذا؟” قد تكون متضايقًا جدًا من أسئلة الطفل، ولكنك أقرب بكثير إلى التعرف على السبب الأكثر احتمالًا: قد تكون قد لاحظت أن الانحراف قد يكون ناجمًا عن روتين عمل غير ملائم أو حالة صحية سيئة للموظف (قصر في البصر)
إذا افترضت عمومًا “خطأ بشري” كالسبب الأكثر احتمالًا واستنتجت تدريب الموظف من هذا، سيقوم الموظف نفسه أو موظف آخر بارتكاب الخطأ مرة أخرى. الأمر نفسه صحيح إذا تم التعرف على سبب خاطئ: إذا توصلت خلال تحليل جذور السبب هو رؤية الموظف ونصحته برؤية طبيب عيون، فمن المحتمل أن يحدث الخطأ مرة أخرى طالما أن الاضبارة بعيدة عن متناول النظر ولا يمكن رؤيتها بسهولة.
الانحراف الثاني: الافتراضات تؤدي إلى عدم كفاية التحقق من التنظيف
أثناء التحقق من التنظيف Cleaning Validation، تم تحديد قيم التعرض اليومية المسموح بها (Permitted Daily Exposure) للمكونات النشطة بهدف تنفيذ إرشاد الوكالة الأوروبية للأدوية (EMA) بشأن تحديد حدود التعرض. بالنسبة لخطوط التصنيع التي تقوم باستخدام نفس الالة (المكنة) لتصنيع عدة مستحضرات، تم اعتبار المادة النشطة ذات الجرعة الأعلى فقط، لأن تقييم الخطر افترض أن المادة النشطة ذات الجرعة الأقل لم يعد من الممكن قياس PDE الخاص بها عندما تتم عملية التنظيف للوصول إلى مستوى مقبول للجرعة العالية. لم يتم تضمين قيم PDE أو قابلية التنظيف أو قابلية الذوبان للمادة النشطة ذات الجرعة الأقل. تم الاكتفاء بالمادة النشطة ذات أسوأ حالة Worse Case مسبقة دون مزيد من التفسير.
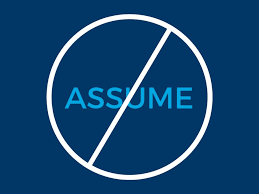
علاوة على ذلك، لم يكن من الواضح من تقارير PDE معايير اختيار أدنى مستوى للتأثير الملاحظ (LOEL – lowest observed effect level) المستخدم.
(المرجع: دليل EU GMP الجزء الأول رقم 5.21 والمرفق 15 رقم 10.6)
المشكلة هي عدم حساب ال PDE لجميع المواد النشطة، لأن الشركة افترضت أنه لن يتبقى شيء بعد تنظيف المادة النشطة A حتى الحد الأقصى للمادة النشطة B، لذا لم يتم اعتبار حساب PDE للمادة النشطة B ضروريًا.

هل يعني وجود 0.00625 ملغ (أو 6.25 ميكروغرام) أن عملية التحقق من التنظيف تامة؟؟
يعتمد الأمر على فعالية/سمية المادة النشطة B,علاوة على ذلك، لم تقم الشركة بمناقشة ما إذا كان تنظيف المادة النشطة B في الواقع جيدًا بنفس القدر وما إذا كان من الممكن بالمقارنة أن تكون هذه الاستنتاجات عمومًا ممكنة. على سبيل المثال، قد تكون المادة النشطة A قابلة للذوبان جدًا في الماء، بينما قد تكون المادة النشطة B قابلة للذوبان بشكل ضعيف – وبالتالي ستظهر الاثنتان سلوكًا مختلفًا أثناء التنظيف.
من تقرير PDE نفسه، لم يكن من الممكن التعرف على قواعد البيانات التي تم استخدامها فعليًا في البحث. لذلك لم يكن من الممكن تقييم ما إذا تم إجراء البحث بالكامل وفقًا لإرشاد وكالة الأدوية الأوروبية بشأن تحديد حدود التعرض. قد استمد التقرير قيمة PDE للمادة النشطة A من LOEL. ومع ذلك، يتطلب دليل وكالة الأدوية الأوروبية الى عدم وجود التأثير الضارno observed adverse effect level (NOAEL) أولاً. إذا لم يتم استخدام NOAEL أو إذا وجدت هناك عدة NOAELs، يجب تبرير السبب الذي يستدعي استخدامه في الحسابات اللاحقة. هذا التبرير غير متوفر.
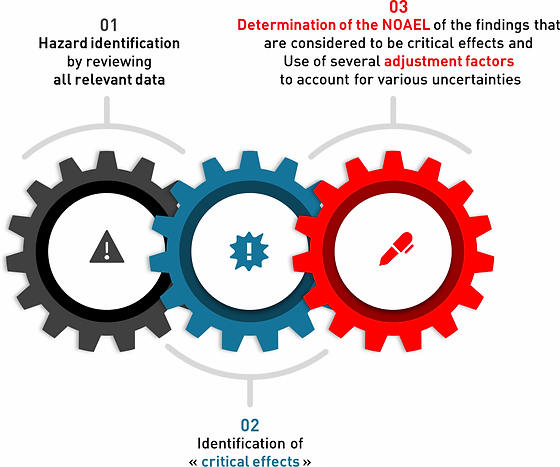
في عالم التصنيع والامتثال، يكمن السر في التفكير بعمق وعدم الاعتماد على الافتراضات. عندما نواجه أخطاءً متكررة، يكون التحليل الدقيق للبيانات وتحليل جذور السبب الحقيقية هما المفتاح لتحقيق التحسين والتطور. الإحصائيات توفر لنا نظرة عامة، ولكنها لا تكفي. يجب أن نسعى لفهم ما وراء الأرقام والأسباب الجذرية للمشكلات.
عندما نلتزم بعدم الاعتماد على الافتراضات، نفتح أبوابًا للتحسين والتجديد. نسعى للتعلم من كل خطأ وتجربة سابقة ونضع استراتيجيات للتصدي للمشاكل بشكل فعال ودائم. تحليل السبب الجذري يسمح لنا بتجنب تكرار الأخطاء والارتقاء بجودة منتجاتنا وامتثالها لأعلى معايير الجودة والأمان.