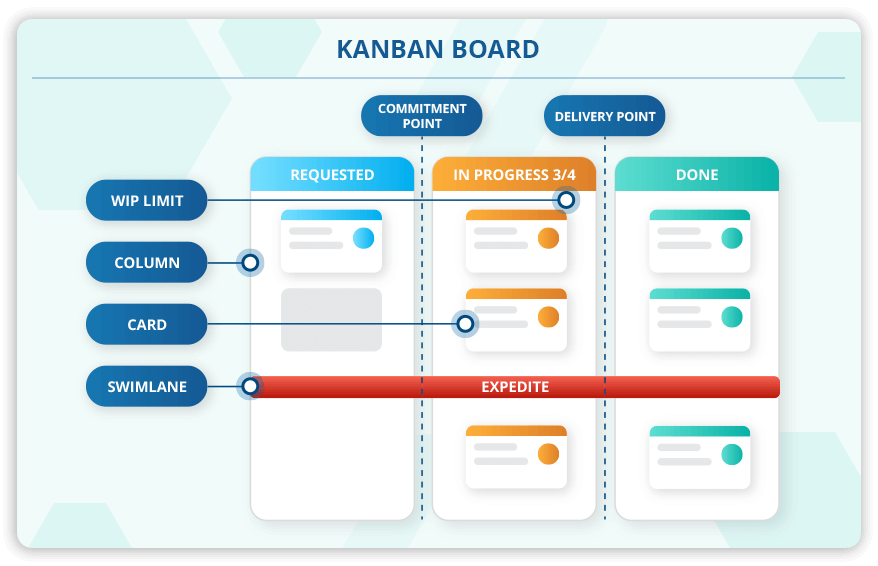
نظام كانبان وتطبيق مفهوم التحسين المستمر: إمكانية التطبيق في التصنيع الدوائي
نظام كانبان هو أداة قوية لتحسين العمليات وزيادة الكفاءة في الإنتاج والإدارة. الهدف الحقيقي من كانبان هو إنشاء نظام مرئي يقلل من الهدر ويزيد من الكفاءة من خلال ضمان طلب وإنتاج الأجزاء الصحيحة في الوقت المناسب.
ويقسم الى ست قواعد أساسية وهي:
- تصور سير العمل (Visualize Work)
القاعدة الأولى والأكثر أهمية في كانبان هي تصور سير العمل بشكل مرئي. يتم ذلك عادةً من خلال لوحات كانبان التي تعرض جميع المهام في النظام وما هي حالتها الحالية. هذا التصور يساعد الفرق على فهم أين يتعثر العمل وأين توجد العوائق.
- تقليل العمل الجاري (Limit Work in Progress – WIP)
لتجنب الإفراط في العمل وعدم التشتت، من الضروري وضع حدود على كمية العمل الجاري. عندما يتم تحديد حد معين لعدد المهام التي يمكن العمل عليها في وقت واحد، يُجبر الفريق على التركيز على إكمال المهام الحالية قبل الانتقال إلى مهام جديدة، مما يعزز الكفاءة.
- إدارة التدفق (Manage Flow)
الهدف هو الحفاظ على تدفق العمل بشكل سلس وثابت عبر النظام. يجب على الفرق مراقبة التدفق باستمرار وضبطه عند الضرورة لضمان أن العمل يتحرك بسلاسة من مرحلة إلى أخرى دون توقفات غير ضرورية.
- جعل السياسات واضحة وصريحة (Make Process Policies Explicit)
يجب أن تكون السياسات والقواعد التي تحكم العمل واضحة ومعروفة لجميع أعضاء الفريق. عندما تكون القواعد واضحة، يسهل على الفريق اتباعها والعمل ضمنها، مما يقلل من الغموض والارتباك.
- التحسين المستمر (Implement Feedback Loops)
كانبان يشجع على التحسين المستمر من خلال دورات التغذية الراجعة المنتظمة. هذه الدورات يمكن أن تكون اجتماعات يومية سريعة (stand-ups)، أو اجتماعات مراجعة أكثر تفصيلاً لتقييم ما يعمل بشكل جيد وما يحتاج إلى تحسين.
- التعاون لتطوير تجريبي (Collaborate for Continuous Improvement – Kaizen)
القاعدة السادسة والأخيرة تدعو إلى التعاون المستمر لتحسين العملية. كانبان ليس نظامًا جامدًا، بل يجب أن يكون دائمًا قيد التقييم والتحسين. الفرق يجب أن تعمل معًا لتجربة أفكار جديدة وتحسين النظام بمرور الوقت، وذلك يشمل تقليل بطاقات كانبان بشكل دوري لتحدي النظام الحالي وكشف مكامن الضعف.
سيساعدك وجود نظام كانبان على تقليل الإنتاج الزائد، والعيوب في الجودة، والتصرف كأنك تقوم بتشغيل عملية مبسطة.
ومع ذلك، يجب أن تفكر في تجنب الحاجة إليه منذ البداية. إذا كنت بحاجة إلى كانبان، فهذا يعني أن لديك مشاكل في الكفاءة لم يتم حلها، ولهذا السبب يُعد ممارسة جيدة تقليل بطاقات كانبان من وقت لآخر لتحدي نظامك الحالي واستئصال أسباب عدم الكفاءة.
لهذا السبب، فإن القاعدة السادسة هي الأهم وتعد محورية في مبادرات التحسين الخاصة بك.
نظام كانبان في التصنيع الدوائي
تطبيق نظام كانبان في المصانع الدوائية يمكن أن يكون مفيدًا جدًا لتحسين الكفاءة وتقليل الهدر وضمان الجودة.
تصور سير العمل (Visualize Work )
لوحات كانبان في المختبرات: يمكن استخدام لوحات كانبان لعرض حالة العينات المختبرية في مختلف مراحل الفحص، مثل الفحص الأولي، التحليل الكيميائي، التحليل الميكروبيولوجي، والتوثيق النهائي. هذا يساعد على تتبع سير العمل وتحديد أي عوائق بسرعة.
تتبع طلبات المواد الخام: يمكن أن تظهر لوحات كانبان في مخازن المواد الخام حالة الطلبات، مما يساعد على مراقبة تواريخ التسليم والحاجة إلى إعادة الطلب.
تقليل العمل الجاري (Limit Work in Progress – WIP)
تصنيع الأدوية: في خطوط إنتاج الأدوية، يمكن وضع حدود على عدد الوجبات التي يتم تحضيرها في وقت واحد. هذا يضمن أن كل وجبة تتلقى الانتباه اللازم لضمان الجودة، ويقلل من احتمال حدوث أخطاء ناتجة عن محاولة معالجة الكثير من الدفعات في نفس الوقت.
التغليف: في قسم التغليف، يمكن تحديد عدد معين من العبوات التي يتم تجهيزها للتغليف في نفس الوقت لتجنب تكدس العمل وتكدس المنتجات في خط التغليف.
إدارة التدفق (Manage Flow)
تصنيع الأقراص: يمكن إدارة تدفق عملية تصنيع الأقراص من خلال مراقبة الوقت المستغرق في كل مرحلة، مثل تحضير الخليط، الضغط، التجفيف، والتلبيس. إذا تباطأت مرحلة معينة، يمكن تحديد المشكلة بسرعة واتخاذ إجراءات لتحسين التدفق.
تحضير الطلبات: يمكن إدارة تدفق تحضير الطلبات من خلال نظام كانبان بحيث يتم تقسيم العمل إلى مراحل مثل اختيار المنتجات، الفحص النهائي، والتغليف. يمكن للعمال مراقبة التدفق بشكل أفضل وتحسين التنسيق بين المراحل.
جعل السياسات واضحة وصريحة (Make Process Policies Explicit)
إجراءات السلامة: يمكن استخدام لوحات كانبان لتوضيح السياسات الخاصة بالسلامة، مثل الالتزام باستخدام معدات الوقاية الشخصية (PPE) في جميع الأوقات، وإجراءات التعامل مع المواد الكيميائية. تكون هذه السياسات مرئية دائمًا، مما يضمن أن الجميع على دراية بها ويلتزم بها.
سياسات الجودة: يمكن أن توضح السياسات المرتبطة بفحص الجودة على لوحات كانبان بحيث يعرف جميع العاملين ما هي المعايير التي يجب الالتزام بها قبل الموافقة على دفعة من الأدوية.
التحسين المستمر (Implement Feedback Loops):
اجتماعات مراجعة الإنتاج اليومية: يمكن إجراء اجتماعات قصيرة كل يوم لمراجعة تقدم العمل، تحديد المشكلات، وإجراء التعديلات اللازمة لتحسين العملية. يمكن أن تتضمن هذه الاجتماعات مراجعة لوحات كانبان لتحديد الاختناقات أو التأخيرات.
مراجعة الأداء الشهري: على المستوى الاستراتيجي، يمكن أن يعقد فريق الإدارة اجتماعات شهرية لتحليل بيانات الأداء وتحديد فرص التحسين، مثل تعديل حدود WIP أو تحسين سياسات العملية.
التعاون لتطوير تجريبي (Collaborate for Continuous Improvement – Kaizen)
ورش عمل كايزن: يمكن تنظيم ورش عمل كايزن لمجموعات العمل المختلفة لتقديم اقتراحات حول كيفية تحسين العملية. يتم تشجيع الموظفين على اقتراح تعديلات في نظام كانبان مثل تغيير حدود WIP أو تعديل تدفق العمل بناءً على تجاربهم اليومية.
تجربة تقليل بطاقات كانبان: من خلال تقليل عدد بطاقات كانبان بشكل دوري، يمكن للمصنع اختبار قدرته على العمل بكفاءة أكبر مع نظام أقل تعقيدًا، مما قد يكشف عن فرص لتحسين العمليات وتقليل الفاقد.